
Injection Molding: A Reliable and Cost-effective Manufacturing Process
Plastic has become an integral part of our lives, and it is hard to imagine a world without it. From containers, bottle caps to automobile parts, plastic is everywhere. One of the key processes used for making plastic parts is Injection Molding. It is a reliable and cost-effective manufacturing process that has been around for decades, and has become the preferred process for producing plastic parts.
What is Injection Molding?
Injection molding is a manufacturing process in which plastic material is melted and then injected into a mold to create a part. The process starts with the material being fed into a heated barrel, which then mixes and forces into a mold cavity by a reciprocating screw or a ram injector. The mold is usually constructed using steel or aluminum, and it is precision-machined to form the features of the desired part. The melted plastic material then cools and hardens to the configuration of the mold cavity.
Advantages of Injection Molding
Injection molding is a cost-effective and reliable manufacturing process that has several advantages over other molding processes. Some of the advantages of injection molding include:
High Volume Production: Injection molding is ideal for producing high volumes of plastic parts due to the ability of making multi-cavity injection molds, where multiple parts are made with one cycle. This makes it possible to produce parts in large quantities in a short amount of time.
Versatile: Injection molding is used to create a wide range of plastic products, from small components to entire body panels of cars. This versatility makes it a popular choice for many industries, including automotive, medical, consumer goods and aerospace.
Accuracy and Consistency: With the use of computer-aided design (CAD) and computer-aided manufacturing (CAM) technologies, injection molding can achieve high levels of accuracy and consistency in manufacturing. This ensures that the parts produced meet tight tolerances and maintain consistency across multiple batches.
Disadvantages of Injection Molding
Despite its many advantages, injection molding also has some disadvantages. Some of the disadvantages of injection molding include:
Expensive Tooling: Injection molding can be expensive due to the investment in tooling, which is required to create the molds used in the process. This can make it less appealing for low-volume production.
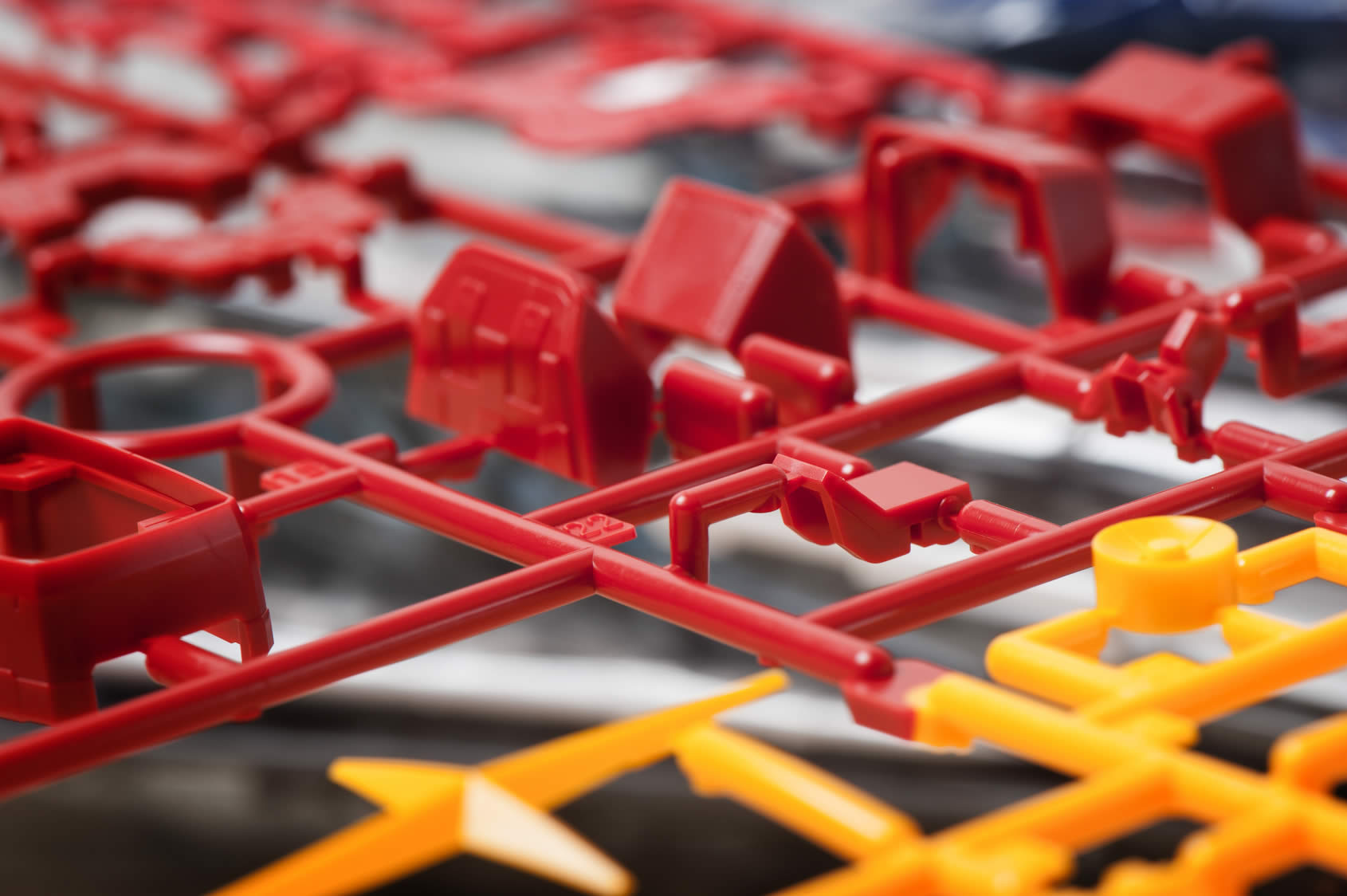
Prototype Requirement: Some custom complex parts may encounter problems during the injection molding process, such as warp. To avoid this, prototyping is needed to identify and correct these issues before production.
Surface Defects: Injection molded parts may experience surface defects such as sink marks, warping or flow marks which can impact the aesthetic appeal of the part. Addressing these issues can add additional time and cost to the production process.
Conclusion
Injection molding is a reliable and cost-effective manufacturing process that has become the preferred choice for producing plastic parts. With its versatility, accuracy, and ability to produce high volumes, it has become a popular choice for many industries. However, it is essential to consider the disadvantages of injection molding, such as expensive tooling and surface defects, before selecting it as your preferred manufacturing process. At ALL STAR PLAST, we provide high-quality injection molded parts for a wide range of industries. With over 15 years of experience, we are committed to delivering reliable and cost-effective solutions for your manufacturing needs.